Rammed earth + Darts
- Scarlett Lee
- Mar 17, 2020
- 3 min read
Updated: Jul 6, 2021
Darts are one of fascinating ways to design and shape fabrics transforming 2 dimensional fabrics into 3-dimensional forms. In the fashion industry, darts are used to create fitted clothes wrapping the human body. In my research, I had an experiment on how dart patterns on fabrics have an influence on the shape of rammed earth.
First of all, I draw dart patterns on fabrics marking where I will sew. A single sheet of a fabric was used stitching each end in order to minimise the rupture of joints on fabrics which could be caused by the tension during the ramming course.
The fabric was stitched following the pattern of darts and vertical folding joint, and it was sat on a timber scaffolding. The bottom and top parts of fabric was tightly fastened with the timber panel and nails to minimise the fabric’s bulging.

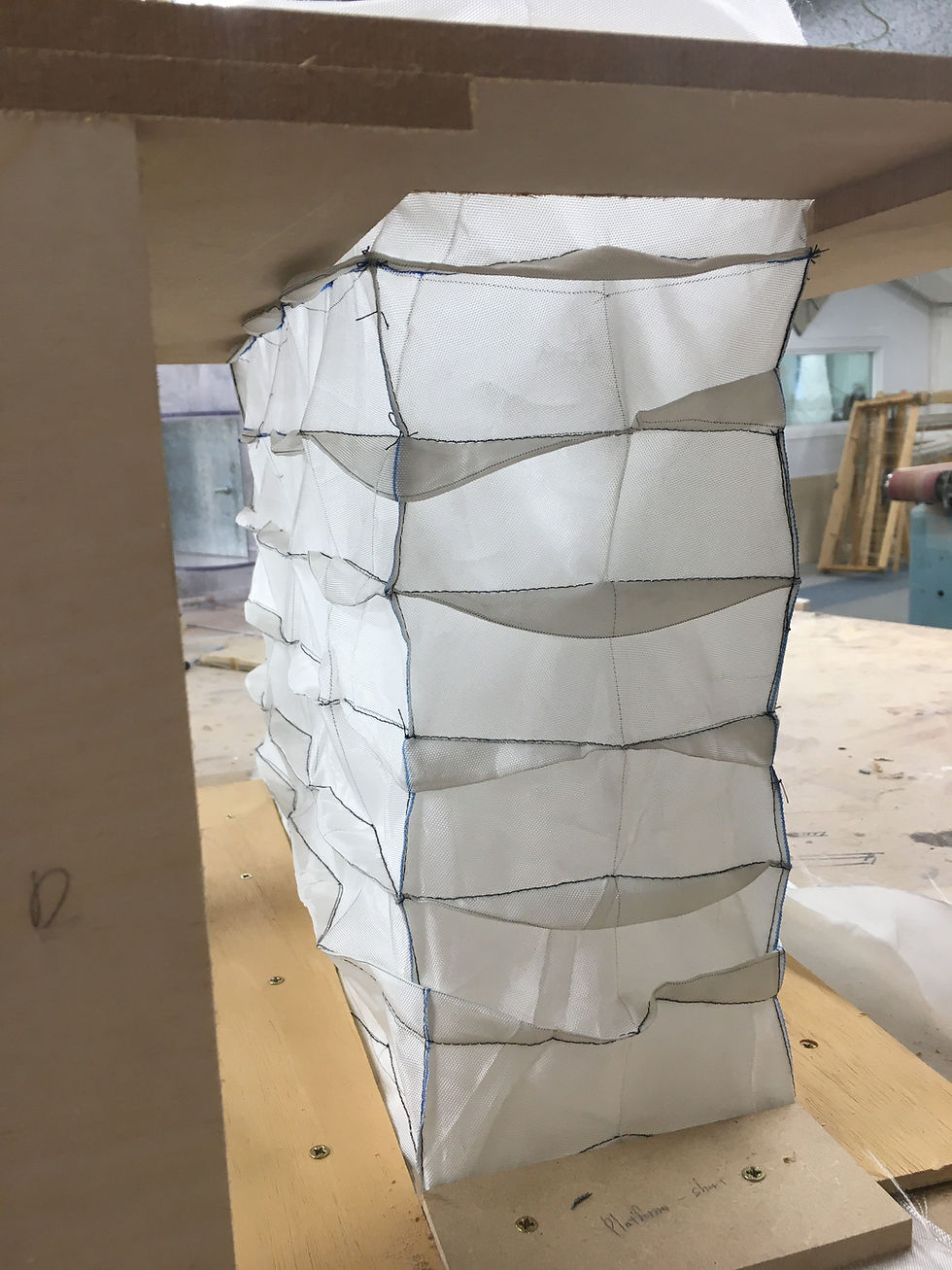
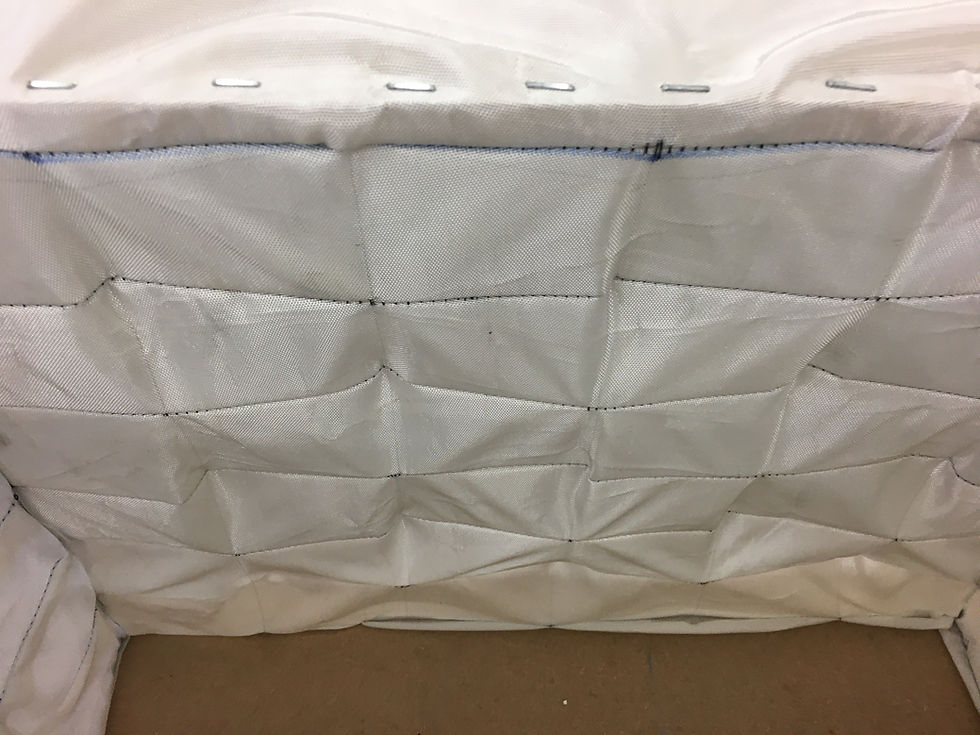
Soils excavated from a construction site was sieved through a mesh size of 20mm. Since these soils were clayey, they were altered being mixed with sands. After conducting the optimum micro-filler effect test, these soil samples have shown the highest density when they are mixed with the ratio of 4 (soil) :4 (sand) or 4 (soil) :5 (sand).
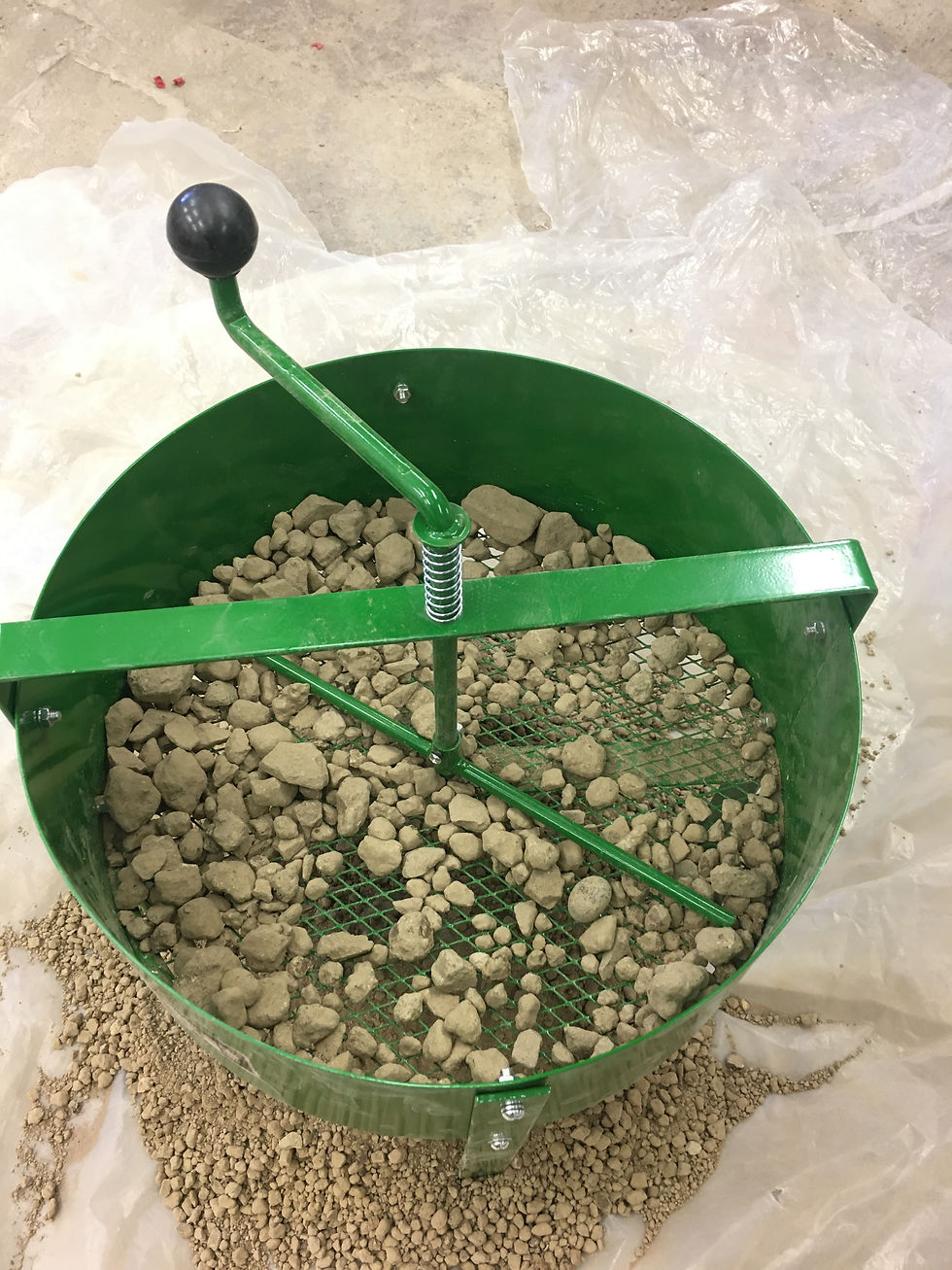

Once a soil mixture having an optimum moisture content has prepared, it was poured on fabric formwork around an 8cm layer and compressed manually with a hammer having a round shaped profile. This shape of hammer played an important role on the outcome of the surface finishing of the rammed earth model eventually. Since fabrics on flexible formwork are bulging and changing its form during the ramming process, it is essential to create a customised shape of a rammer accordingly.


As rammed earth is almost reaching the top of the formwork, it was quite hard to compact soils with a rammer since the top of the fabric was tilted tightly as the middle part of the fabric bulged out. So, I pressed hard with fingers the areas which cannot be reached with a rammer. Through this, I realised that the morphological change of fabrics during the ramming course is one of significant aspects I have to consider about when I design fabric formwork in the future especially for large scales.
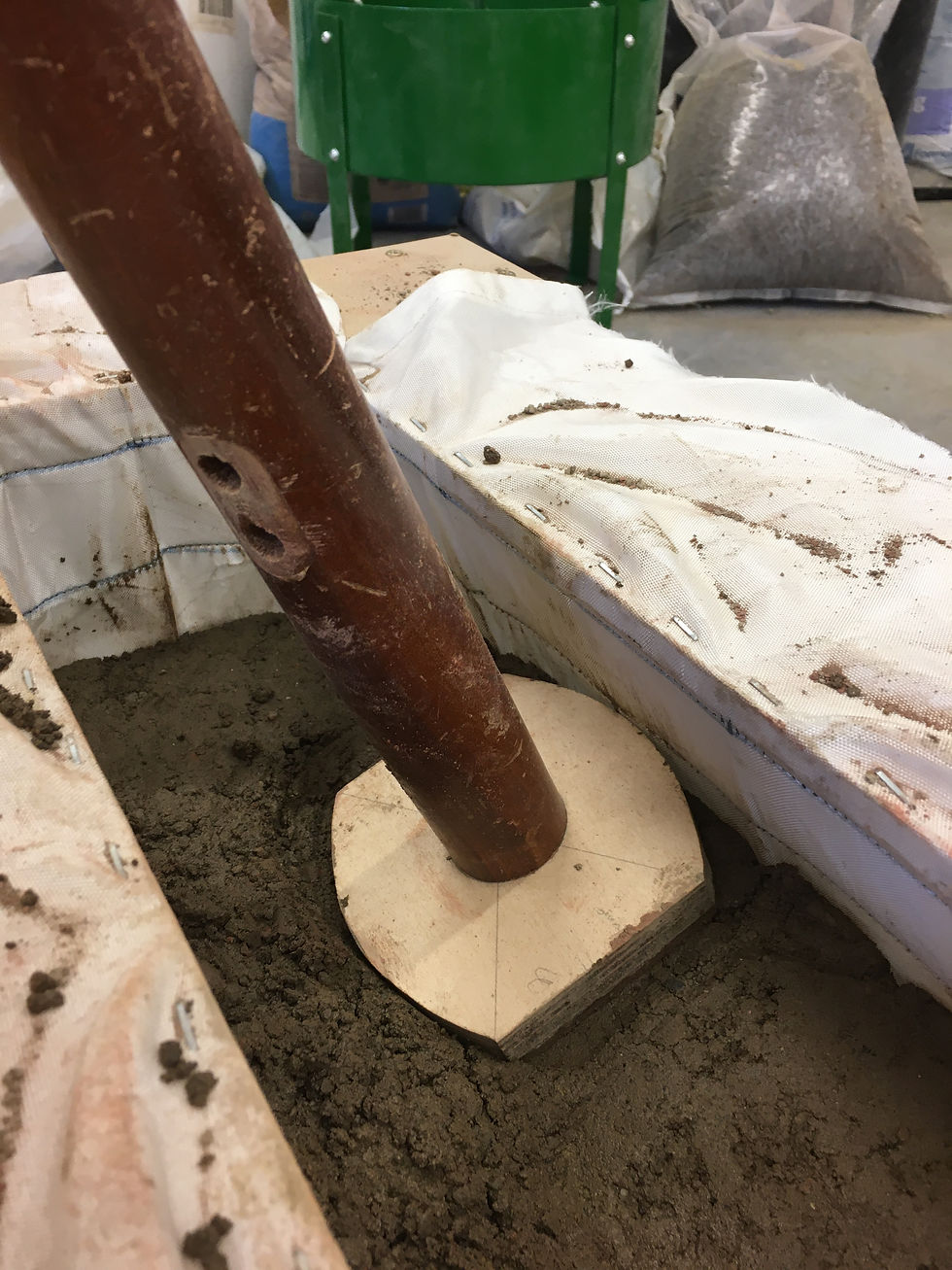
After ramming is finished, when I touched the surface of fabrics, it was pretty cold and wet. I assume that this permeable fabric helps to increase the density of rammed earth evaporating moistures on soils more easily than rigid formwork, though it needs to be proven through a test in the future.
When I examine carefully the profile of the rammed earth model just after the ramming course, the two narrow sides of the rammed earth picked up the curvature created by darts quite successfully. On the other hand, it was not very clear that the pattern of darts was embedded on the wider sides of the rammed earth model.
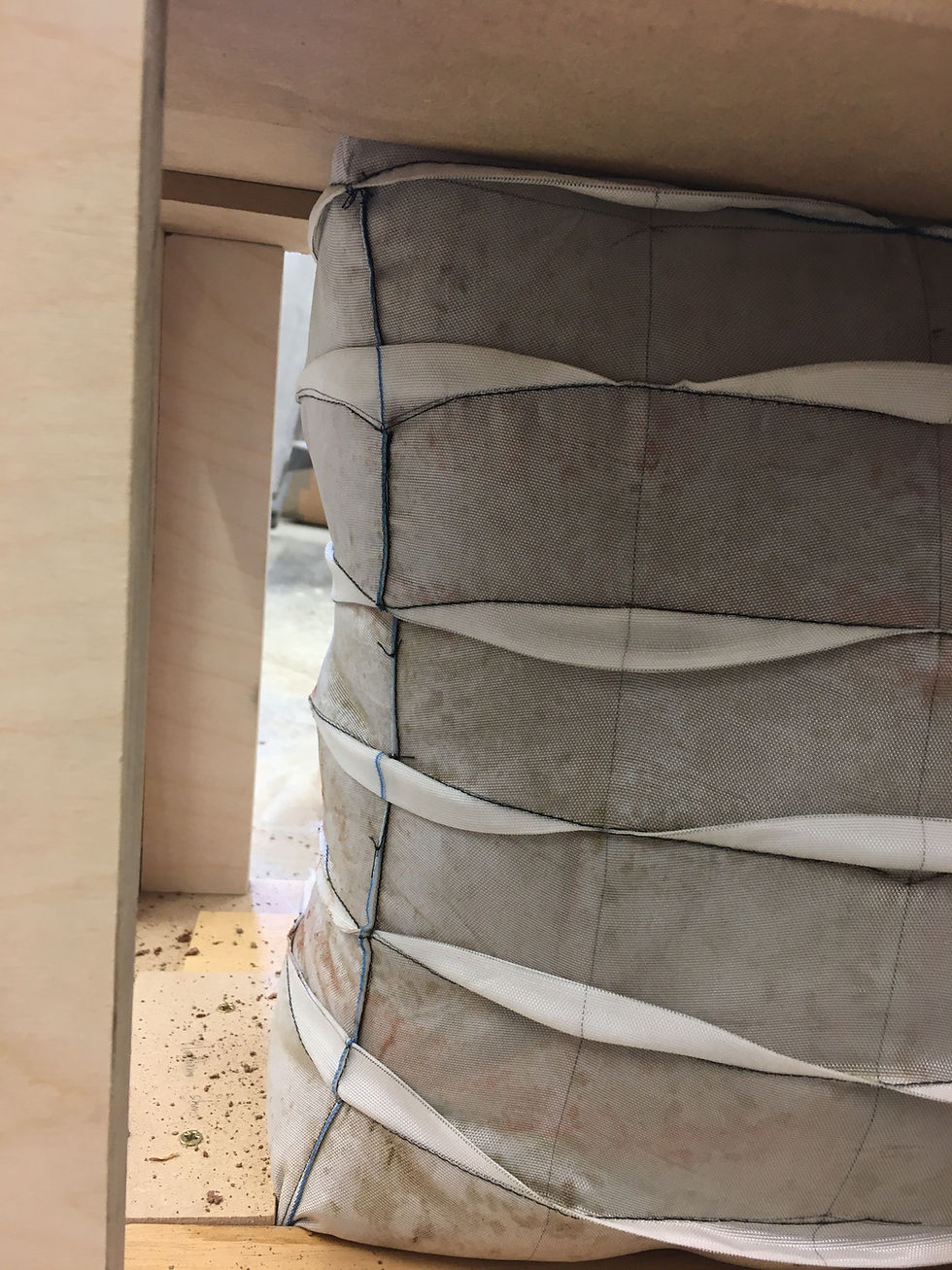

Just a day later completing the rammed earth model, I dissembled the fabric formwork. After unscrewed all the wooden panel joints, I’ve cut the fabric joints carefully with a scissor. Interestingly, the seam of the fabric was imprinted on the surface of rammed earth as a straight line. Although it was quite subtle, the wide facade of the model expressed the dart pattern relatively well. What was more interesting was the narrow sides of the model. Very fine details of fabrics, not just the pattern of darts but also wrinkles, were incredibly transferred on the façades of the rammed earth.




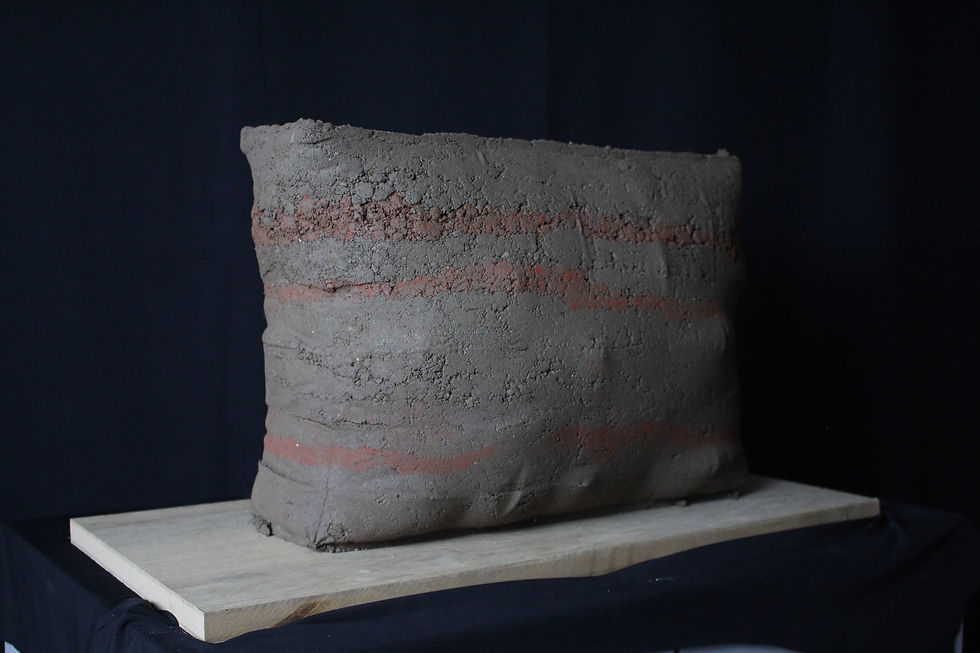


Through this model, I found very interesting aspects to explore more. One of them is that the pattern of darts since different effects and results could come out according to the distance of pattern or size of darts even with a same pattern. Another aspect is the behaviour of fabrics of flexible formworks. As I mentioned previously, fabric formwork shows a great morphological change before, during and after the ramming process, which is a fundamental difference from rigid formwork. Since the bulging of fabrics is inevitable, it will be the key to the design of fabric formwork considering how much bulging will be allowed, how it will be controlled, and how it is manipulated for design.
コメント